Where are protective screens used?
Protective screens are always used if the safety of the production process or the quality of a product could be endangered by an impurity. Protective screens can therefore theoretically be used at every stage of the process, but there are some typical applications
For the delivery of raw materials and before product storage
Many businesses have their bulk goods delivered by tanker or silo vehicle. So, while the product is being emptied and, for example, put in temporary storage in silos, screens on the tanker can be used for protective screening. These can easily be installed in the vehicle’s conveyor pipe and ensure that contaminants and impurities don’t make it as far as the silos, let alone the production process. Protective screening makes sense at this stage if the product is to be placed in interim storage for a long time so that no biological impurities can spread, for example.
Before the use of raw materials in the production process
Screens placed at this stage serve as protection for the downstream production machinery. They also contribute to a consistent product quality, as many bulk goods cease to be easy to process if they are not of an adequate quality. In this case, protective screening frequently occurs directly after discharge from the silo. As many bulk materials are prone to agglomeration if stored for a long time, protective screening makes sense even if the product was already screened before storage. The agglomerates created are separated by a protective screen after discharge from the silo, and light clumps are even dissolved by the screening.
Often, the raw materials aren’t placed in interim storage but removed immediately from their transport containers, e.g. Big Bags, and fed straight into the production process. In these cases, Engelsmann protective screens can even be integrated directly into the emptying station. This saves valuable installation surface area.
Before packaging the merchandise
It should be ensured that the product is free of all unwanted elements at the latest before the product is packaged or bottled for sale or internal processing. Undetected left-over impurities have a direct effect on the quality of the final product and can, at worst, entail complaints or product recalls.
Why is a protective screen important?
Reliability
As protective screens are usually permanently integrated into the production process, a defective machine can quickly lead to stoppages in production. If a protective screen is used as the “last line of defense” before packaging, production will, at worst, come to a standStill when the protective screening machine breaks down as the quality of the final product can no longer be guaranteed. Engelsmann therefore relies on long laSting machines of a solid construction (made from stainless steel as standard). To avoid downtime, we also emphasize low maintenance constructions with few parts subject to wear.
Throughput performance
If protective screening is implemented before the material feed in the production process, the productivity of the downstream processes depends greatly on what level of throughput the screen attains. If the screen does not achieve the required throughput performance, not enough material will be available for production. The throughput performance of a protective screening machine must be precisely coordinated with the production process so that the right quantity is available at the right time. At businesses where large quantities of bulk goods are processed, protective screens with high throughput performance are often in demand. Therefore, Engelsmann offers various models of protective screens with different throughput performance levels.
HOW DOES SILO SIFTER WORK?
Generally, solid fluids that come in bulk with silobus must be subjected to a control and separation before entering the process.
This is especially important for food processes (flour, sugar). Thus, foreign substances are separated and as a result of this separation, they become ready for use.
One of the types of sieves we have produced is the silobas control sieve for such processes.
While transferring with the help of high pressure (1.00-1.50bar), the product is separated from foreign substances with the help of vibration. All parts that come into contact with the product are certified according to regulation (EU) 1935/2004 or regulation.
Although the sieve is designed to work under pressure, it can also be used in vacuum processes.
Technical specifications
Easy to Clean Pneumatic Line Sieve
Length: 1.000mm, Width: 1.000mm Height: 1.500mm
Sieve diameter: Ø800mm
Sieve cleaning area: 0.5m2
AISI304 Stainless Food Suitable Construction
Capacity 7-12 tons / hour flour (for 200 µm flour) Capacity is directly proportional to the sieve mesh size.
Sieve Permeability: 1.000-3.000 µ
Operation Type: Pneumatic conveying systems operating under vacuum and pressure (-500, + 1.5bar)
Capacity is directly proportional to screen mesh size.
Pipe Connection: 60.3-114mm
Motor Power: 0.18--0.37kw direct coupled 1.500rpm, 380V, 50Hz Motor, IP66 ATEX
Easily removable inner screen structure, automatic cleaning feature, Hinged cover.
Silobas inlet camlock adapter, Standard Input-Output Pipe Size: 60-114mm
Important Note: Lobe blowers - can be used with low pressure compressors. Sieves increase the vacuum and pressure values by making a negative effect on the system. If it is to be used in the flour system, bran and mix flour should not be passed through it without changing the inner sieve.
For more information;
h
Mini automation panel with pressure transmitter showing the pressure inside the screen
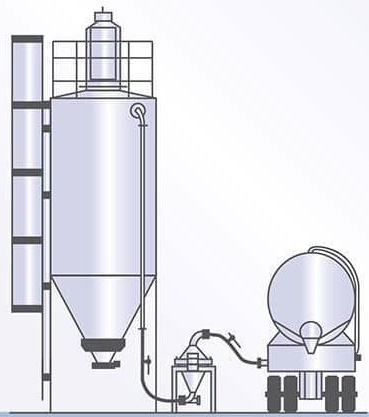
Vibration Screen, SiloTruck Screen, Silo Screen
We also apply vibration and conical pneumatic screening technologies
in your pneumatic transfer processes and silobuses. Thanks to the
conical screens in the range of our products which are installed at
the highest level of the silos, we prevent ingress of foreign
objects into your silos. Foreign materials especially sand, calcite
and similar materials in the construction chemicals may give damage
to the screws and mixers, other transport equipment of the process.
For this reason, the raw material introduced in the process should
be screened definitely.
Sieving - Maximum control for optimal
results
Companies in the food, feed, pharma and chemical
industries are being confronted with increasingly stringent
requirements with regard to food safety, quality, tracking & tracing
and hazards associated with dust and explosions. So it should come
as no surprise that Dinnissen Process Technology is continually
searching for the best solutions when it comes to quickly and
reliably managing various granulated as well as powdered materials.
Effi cient fractionation ensures the highest purity Our sieving
technique is based on the use of our centrifugal sieves. The
material to be fractionated is brought into the sieving
chamber,
where the material is agitated by spinning fi ns. Those fractions
which consist of small enough particles pass through the centrifugal
sieve, whereas contaminants and larger particles are quickly
transported onwards. By varying the rotation speed as well as the
diameter of the openings and the path length of the sieve, we can
realize any desired sieving result. And our broad range of
accessories and options makes it possible to realize the necessary
level of quality, safety and hygiene for any situation.
PDF
brochure

HYGENIC DESIGN SIEVE
The machine housing and the screens are completely made of
stainless steel. A new tangential inlet without screws prevents
product from accumulating in the inlet. This makes the inline
check sieve the perfect choice for use in the finished product
section.
SPECIAL DESIGN SIEVE
The mobile screen is connected between the
tanker truck and the silo-loading line using quick-change
couplings. Pneumatic conveying can now be started.
The
vibratory flatbed screener gently control screens the material
with minimum particle degradation. The screen mesh width can be
chosen according to the material to be screened. Fine particles
surpass the screen, impurities remain on the screen.
After
finished operation, the screen can be easily cleaned off by
simply tilting up the entire top of the machine, either manually
or using a vacuum cleaner.
Tr
- Lebels: sieve, flour sieve, flour sifting, powder sieve, contitinuous sieve,rotary sieve, ,cyclone,inline sifter, inline vacuum sifter, pneumatic conveying sifter, Centrifugal Sifter, rotary sifter,flour sifter,sieve,screening,screen, Pneumatic Conveying Cifter | Inline Rotary Sifter | Inline Sifter | Vacuum Sieve | Pneumatic Conveying Screening